OMRON Corporation (HQ: Shimogyo-Ku, Kyoto. CEO: Yoshihito Yamada) will introduce on July 1, 2016, the IO-Link compliant Photoelectric Sensors E3Z, Color Mark Photoelectric Sensors E3S-DC Series, Proximity Sensors E2E and E2EQ Series, and IO-Link Master Units GX and NX Series all at once as a first step of integrating sensors into the IoT (Internet of things), ideal for use at manufacturing sites. This launch of the IO-Link compliant sensors is a big step in making production equipment smarter to add various information and communication functions to over 100,000 of specifications of control components for factory automation (FA devices) and achieve integration of FA and ICT (information and communications technology).
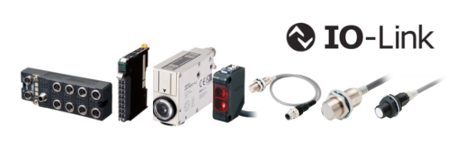
IO-link is a standardized technology for sensors and actuators communicating with I/O terminals, specified in the international standards, IEC 61131-9. A major Japanese automobile manufacturer has decided to implement the IO-Link with EtherCAT as a standard network to adopt the IoT for its factories and has recommended the use of compliant devices to suppliers around the world.
At present, as manufacturing industries accelerate their shifts to high-mix low-volume production and optimally located production on a global scale, there is growing demand for adopting the IoT to production lines and equipment in order to improve operation rates of production equipment and produce high quality products stably. Given such circumstances, in order to visualize not only sensors’ ON/OFF signals but also other information such as light incident levels, OMRON adds IO-Link technology to Photoelectric and Proximity Sensors, for which OMRON has a high market share, used in many areas at manufacturing sites. The new IO-Link compliant Sensors equipped with individual identification functions and OMRON’s unique abnormality detection and condition monitoring functions allow reduction in equipment downtime, a decrease in the frequency of sudden failure, and improvement in changeover efficiency, which are management challenges at manufacturing sites. OMRON contributes to making production equipment smarter by providing the IO-Link compliant devices which enable a host controller such as a PLC to gather various data crucial for stable operation of the equipment through the Master Unit via EtherCAT.
Value Provided to Make Equipment Smarter
1. Individual Identification Function to Improve Changeover Efficiency
With the individual identification, you can easily check mistakes such as misconnected or unconnected sensors and installation mistakes. Because it is possible to program multiple sensors at once using the command language from a host controller, it is also possible to reduce commissioning time and changeover time sharply.
2. Abnormality Detection Function to Reduce Equipment Downtime
When errors such as disconnections and short circuits in wiring cables of sensors occur, faulty parts and such phenomena are notified to a host controller in real time. It is easy to identify the cause of equipment stoppage, which makes it possible to recover the equipment in the shortest amount of time.
3. Condition-Monitoring Function to Achieve Predictive Maintenance without Stopping Operation of Equipment
The Proximity Sensors alert you of their detection conditions before false detection or failure occurs due to detection position changes caused by wear and vibration in equipment components. This enables predictive maintenance to reduce the occurrence of unexpected errors of the equipment.
The Photoelectric Sensors monitor their light incident levels. This makes you understand unstable situations of the incident levels due to the influence of dust and water drops in real time to reduce the risk of abrupt stoppage by carrying out maintenance before false detection occurs.
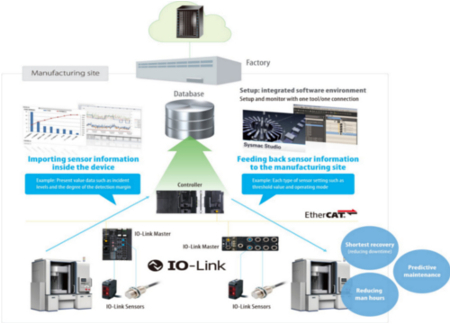
OMRON brings innovation to manufacturing sites through automation with “integrated,” “intelligent” and “interactive” concepts. OMRON has been developing and providing FA devices required for various manufacturing sites for many years and continuing to provide customers with benefits of global standard information technology by actively using open networks such as EtherCAT and IO-Link. OMRON will continuously advance automation with the “intelligent” concept and contribute to making production equipment smarter by adding OMRON’s unique technical know-how cultivated at its manufacturing sites to a wide range of development know-how for FA devices and know-how in data application with open networks and expanding its lineup of the FA devices connectable to the IO-Link.
ABOUT OMRON CORPORATION
Headquartered in Kyoto, Japan, OMRON Corporation is a global leader in the field of automation. Established in 1933, and headed by President Yoshihito Yamada, OMRON has more than 37,000 employees in over 35 countries working to provide products and services to customers in a variety of fields including industrial automation, electronic components, social systems, and healthcare. The company has five regional head offices in Kyoto (Japan), Singapore (Asia Pacific), Shanghai (Greater China), Amsterdam (Europe, Africa, and the Middle East), and Chicago (the Americas). For more information, visit OMRON’s website: http://www.omron.com/